Originally published in the Carolina Fire Rescue EMS Journal in February, this article highlights how S&T and Texas Tech University (TTU) are joining forces to give a classic piece of gear a modern update. Reprinted with permission.
We expect a lot from firefighters. Time and again, they rise to the challenge: meeting communities’ growing needs, expecting the unexpected, and adapting in real time—often under extreme pressure. And if we expect them to adapt, we should expect their protective gear to evolve with them as well. Responders need effective, affordable equipment that they can rely on to support their increasingly demanding jobs.
Additionally, with a changing response landscape, the roles and responsibilities of firefighters have changed significantly in the past few decades. Firefighters are required to perform structure firefighting, search and rescue, hazardous materials mitigation, and disaster response—but it doesn’t end there. The increased call for firefighters to respond to potentially violent emergency events (with or without law enforcement) such as active shooters, terrorist incidents, or armed crowds, demands better physical protection.
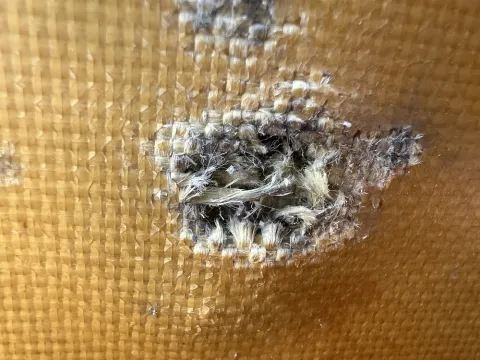
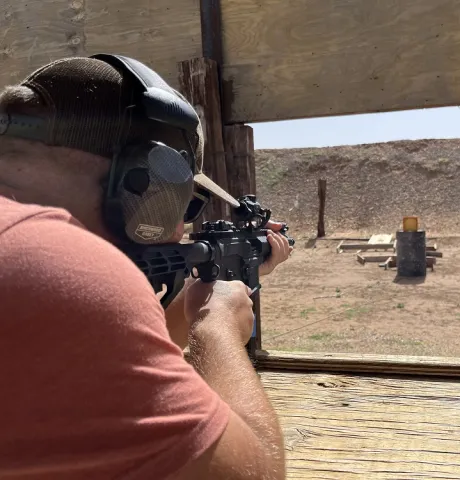
Perhaps no other item is more classically associated with firefighters than their helmet. It is a highly valued piece of equipment that can even hold special emotional significance for a firefighter—providing a sense of not only safety but also confidence when donned. Paradoxically, though, according to the National Fire Protection Association (NFPA), roughly 40% of musculoskeletal injuries reported by firefighters can be attributed in part to the helmet—the very thing that’s supposed to protect them. Though designed to shield the firefighter’s head from thermal and low-velocity direct impact, helmets often contribute to overexertion/sprain-related head and neck injuries because of the added bulk and weight. Helmet-related injuries were also the subject of a 2015 lawsuit in St. Petersburg, Florida, where firefighters claimed the helmet design caused neck and head injuries.
An effective, modern firefighter helmet calls for thermal and ballistic protection combined with communication devices, face shield, visor, thermal imaging, and lighting. However, all of these elements increase the total weight and potentially shift the helmet’s center of gravity. Thus, these changes can lead to injuries to the cervical spine and neck muscle fatigue.
Traditional structural firefighter helmets do not incorporate these enhanced capabilities, nor do they offer sufficient ballistic protection. As a result, firefighters currently either forego ballistic protection entirely or they have two helmets, one for structure firefighting and one for violent situations. This means twice the amount of gear to procure, transport, store, and maintain. It is simply not practical, and it could be dangerous during a rapidly evolving response in which the firefighter must remove one helmet and replace it with the other. That’s why the Department of Homeland Security (DHS) Science and Technology Directorate (S&T) is developing an all-in-one solution that is both protective and light—providing adequate functional mobility as well as positional stability, thereby reducing the risk of injury, while also supporting ancillary accessories that expand firefighters’ capabilities.


Creating a Helmet That’s Both Protective and Light
To meet this need, S&T is partnering with TTU to develop the Next Generation (NextGen) Firefighter Helmet. This new, cutting-edge piece of technology will provide both fire and ballistic protections and mitigate the risk of blunt head trauma. It will incorporate both NFPA 1971:2018 fire protection and National Institute of Justice (NIJ) Level IIIA ballistic protection. As the research and development arm of DHS, S&T partners with private industry and academia to develop innovative solutions to the most pressing challenges faced by first responders. TTU is an internationally recognized research institution with an award-winning faculty. According to S&T program manager Maua Karen H. Johnson, “Both S&T and TTU are anticipating an incredibly positive impact with this project.”
The new device will employ alternative materials and advanced ergonomic design solutions that eliminate the risks of the conventional helmet system. It will not only expand the range of protection for firefighters by delivering an injury-mitigating helmet; it will also promote new safety standards and advance the collective knowledge of material design.
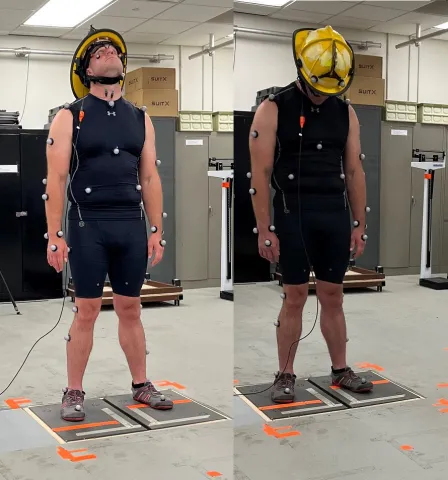

The project is already well underway with the ultimate goal of producing a prototype capable of performing with high fidelity in operational environments later this year. Initial critical design analyses examined the capabilities and limitations of existing helmets, including functional mobility, dynamic positional instability, skull area covered by the outer shell, head-helmet contact pressure, peripheral visibility range, and other factors and parts that can contribute to the risk of head and neck injuries.
The NextGen Firefighter Helmet will be designed with a shell that can absorb energy during impact and rapidly dissipates it without injuring the skull or brain. While the current materials used in both firefighter and military helmets are inadequate for the temperature and ballistic protection being sought, they provide a useful blueprint for future innovation. For example, Kevlar fiber has a melting point of 1040 °F and has proven highly effective in ballistic helmets and body armor. Similarly, polyester resins used in current firefighter headgear can have glass transition temperatures (the point at which it becomes hard and brittle) as high as 386.6°F. The idea is that thermosetting resins can be reinforced with Kevlar fiber, creating a shell that meets both the thermal and ballistic protection requirements of the NextGen Firefighter Helmet.
Another important aspect of the design is the center of gravity and subsequent stability. The helmet must provide both static and dynamic fits to protect from blunt impacts. While there has been significant research on assessing injury-mitigating design solutions for both military and motorcycle helmets, there is a lack of pre-existing systematic research on designing a user-centric injury-mitigating firefighting helmet, including ballistic protection, that addresses firefighters’ concerns.
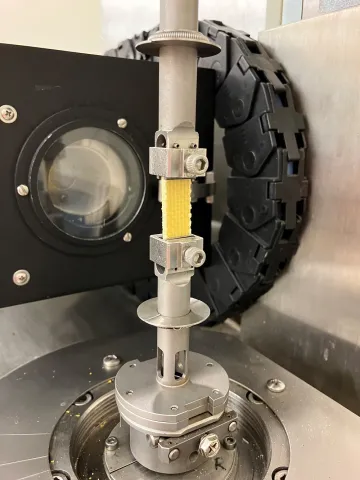
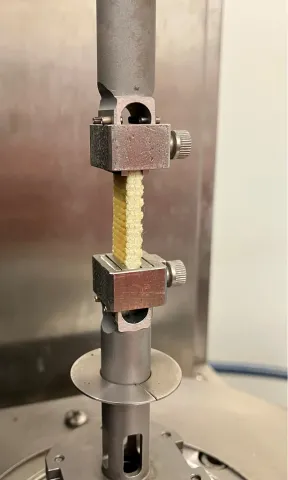
Ensuring End-User Needs Are Considered Every Step of the Way
The NextGen Firefighter Helmet project is seeking to address all of these concerns. Firefighters’ insights are being incorporated throughout the entire development process. To that end, researchers from TTU’s Industrial, Manufacturing, and Systems Engineering Department designed and distributed an online Firefighter Helmet and Safety Survey to collect feedback on various helmet features that support or hinder overall safety and functionality. The questionnaire helped assess the safety, functionality, and overall satisfaction of existing firefighter helmets. It included an additional supplementary portion (completed by over 100 responders) for those who have experienced a head injury or concussion in the past. All of the more than 1,700 responders to the survey were firefighters currently working or volunteering in a local fire department in the United States.
In addition, the head and neck biomechanical data of 36 firefighters was recorded in a study conducted by TTU in September 2022. Researchers are using this information to help determine optimal ergonomic designs for a prototype that will both improve usability and reduce the risk of head and neck injuries. Participants in the study were also evaluated for endurance with and without wearing a helmet to gauge neck flexion and extension limits. Sustained exertion was calculated to determine the type of helmet shape that causes the smallest reduction in endurance and the least amount of fatigue. The goal is to achieve improved mobility, visibility, comfort, and fit while also reducing neck muscle fatigue, skull vulnerability, and cervical spinal load.
Despite all of the innovations being sought for this new piece of gear, researchers are keeping in mind the end-user desire for ease of use. The NextGen Firefighter Helmet will be employed in nearly the same manner as current helmets. The firefighter will have the helmet on or near his or her person when responding to a call. Upon arriving at the call scene, the firefighter should be able to put on their helmet, mask, and hood in under one minute. Establishing communication and performing a communications check with an integrated communication module should be no more complicated or difficult than with current solutions. When entering a structure, activating integrated lighting should be simple, easy, and quick. The new helmet should require few, if any, changes to current standard operating procedures.
Evaluating Prototypes Under Strenuous Conditions
Researchers are hard at work on prototypes that put all of this data and feedback into practice. They are engaging a combination of principles and methods from four key areas—reverse engineering, materials design, injury biomechanics, and human factors engineering. The testing environment contains state-of-the-art equipment such as a Delsys TrignoTM Wireless electromyography system, 10-camera Eagle optical digital motion capture system, and Pupil Core eye-tracker. The high-speed desktop computers have Abaqus finite-element modeling software to develop human head and neck models, HyperMesh to process helmet imaging data, and open-source OpenSim musculoskeletal modeling software to develop head and neck biomechanical models. Using all of these resources plus extensive expertise, they have developed a digital prototype of the NextGen Helmet for ballistic protection tests and biomechanical modeling. Frontal, lateral, and crown impacts have been successfully simulated to analyze potential brain trauma from various projectiles such as .44 Magnum bullets. Additional evaluation is ongoing to help further optimize the design.
The TTU team collaborates with the Department of Chemical and Biomechanical Engineering at North Carolina State University (NCSU) to fabricate physical prototypes—approaching different vendors to identify cost-effective materials able to withstand impact and penetration resistance testing, as well as thermal trials. Just recently, they successfully produced a 10.01 mm helmet shell using a vacuum bagging process, manually applying resin to the fabric to facilitate the infusion. To complete this work, the team has access to an Advanced Manufacturing and Materials Lab (AMML) equipped with additive manufacturing equipment capable of fabricating prototypes and applicable parts from plastic, metal, ceramic, and composite materials. The AMML has two general mechanical testers and one nanomechanical tester with testing capabilities for tensile, compressive, bending, indentation, wear, and scratching tests. The team is also making use of additional laboratory space designed for polymer and soft matter physics and thermal analysis activities. These spaces are outfitted with rotary rheometers (measurement devices to evaluate how a dense fluid flows in response to applied forces), large ovens capable of accommodating vacuum bag molding equipment to manufacture composite panels and helmet shells, atomic force microscopes, and calorimeters (used to characterize glass transition temperature).
Delivering a Worthy Product
The NextGen Firefighter Helmet will meet a variety of key performance parameters. In addition to NFPA 1971:2018 structural firefighting requirements and NIJ Level IIIA standard for ballistic protection, it will also meet the NFPA 1951:2013 protective standard for technical rescue incidents, and United States Occupational Safety and Health Administration 1910.156 fire brigade standard. It will integrate with a variety of self-contained breathing apparatus masks and communications systems and will not inhibit the user’s hearing or vision. Additional desirable characteristics include weight of 62oz or less for size large and 57oz or less for size medium, comfortable, adjustable, maximized range of motion, no snag points, and easy to don and doff.
Once the prototype is ready, likely in mid-2023, an operational field assessment will take place with coordination by S&T’s National Urban Security Technology Laboratory. Firefighters will be brought in to evaluate every aspect of the helmet’s design and capabilities. The ultimate goal is commercialization. The NextGen Firefighter Helmet team also plans to apply for the device to be added to the DHS Federal Emergency Management Agency Authorized Equipment List and seek Support Anti-Terrorism by Fostering Effective Technologies Act of 2002 certification as a final deliverable. TTU’s Office of Research Commercialization will assess the final product, file patents as appropriate, and help accelerate licensure to a commercial partner or university start-up which will bring the technology to market.
For related media inquiries, contact STMedia@hq.dhs.gov.
For more information about S&T’s first responder research and development portfolio visit https://www.dhs.gov/science-and-technology/first-responders-capability.
Correction notice: three photo captions have been edited to credit NCSU, a reference to NCSU's contribution to this project has been added, and "biomechanical data of 11 firefighters was recorded..." has been updated to "biomechanical data of 36 firefighters was recorded..."